Giving Old Machines a Smart Upgrade
A Singapore facility belonging to a major U.S. based medical device manufacturer produces critical, life- saving equipment for patients across the world. In this environment, quality and productivity are essential—both for the success of the company and the health and safety of its end users.
The plant relied on 20-year-old, obsolescent production equipment that was no longer supported by its manufacturer. As these machines began to fail, the unplanned downtime they introduced took a major hit to plant output.
An internal analysis revealed there was no sustainable path to equipment upgrades. The plant needed
to improve performance on these legacy machines and build a smart control layer on them to help restore full productivity.
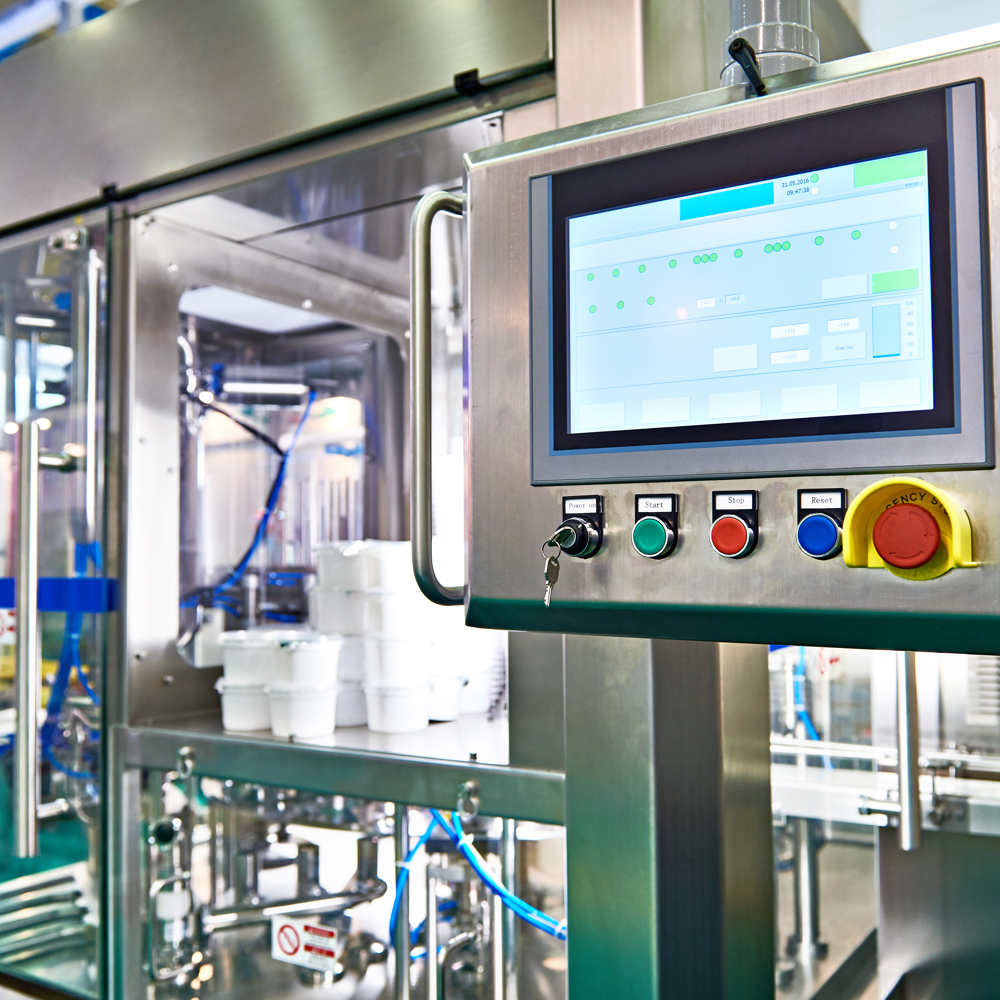
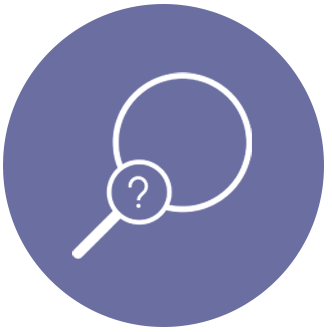
The Problem
With machines this old, there are bound to be issues. The problem here, though, was that the machine diagnostics repeatedly failed to detect these issues or provide root cause for faults. Consequently, while on-device HMIs did stop production whenever faults occurred, maintenance engineers were left with no information to guide them on repairs. The only option was manual diagnostics and trial-and-error card replacements on the faulted machines to get them back into production—often a 2-3-week operation that required the work of two engineers.
With failures like this occurring 2-3 times per month, the unplanned downtime took a major toll on production, pulling overall equipment efficiency (OEE) down to 85% - an unacceptable level for this facility.
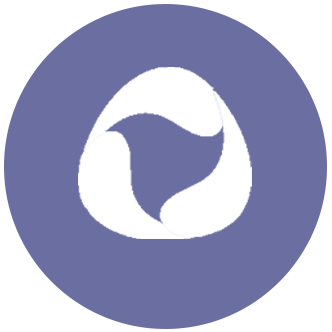
Our Role
This case presented a complicated array of challenges. To return to operational efficiency, the company would need to retrofit its equipment with new drives and a new control system offering the robust diagnostic capabilities required to reduce unplanned downtime and get machines back in operation without a major overhaul. This would require a systems integrator with a unique set of attributes—deep familiarity with production equipment and the components, platforms, and interfaces they use; extensive experience in critical production environments; and the ability to provide whole-package turnaround on the project.
With decades of experience in production environments and industry-leading expertise in the widest range of operating systems, only RoviSys was positioned to take on a project of this scale with so much at stake.
The plant relied on obsolescent, unsupported production equipment. As these machines began to fail, the unplanned downtime they introduced was a major hit to plant output.
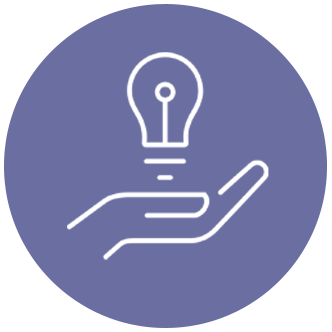
The Solution
After an extensive study of the machines, systems, and plant environment, RoviSys recommended a range of upgrades that targeted both sides of the underlying problem: machine stability and diagnostics.
For the first challenge, RoviSys implemented an upgrade from the plant’s PLC5 control system to Controllogix and the integration of several new drives that offer direct compatibility with the legacy equipment. These drives—Kollmorgen AKD Servo Drives and Lexium SD3 Stepper Motors Drives—were selected specifically to improve equipment performance and stability, offering better functionality and improved cycle times over the current installations. Calling on its vast experience in this market, RoviSys was able to tune these drives to optimal parameters, resulting in reduced operational jerk and smoother
response, thereby improving line stability and reducing fault rates in the machines.
To resolve the diagnostic issue, RoviSys deployed a new visualization system that provides remote IO fault detection. This software upgrade enables the Human/Machine Interface system to precisely pinpoint the exact location of faults occurring in any of the line’s equipment, eliminating the need for productivity-killing trial-and-error manual diagnostics.
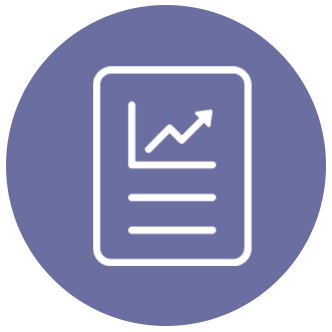
The Result
With these initial improvements in place, the machines and equipment producing these life-saving devices are far more stable and serviceable than ever before. The elimination of manual diagnostics and the reduction of unplanned downtime that this project produced brought the plant’s OEE up to 92%. The new drives also led to a 5% improvement in cycle time per unit on the same machines that had been running for 20 years. Together, these enhancements resulted in an estimated ROI of just 6 months.
And the plant isn’t done yet. After the completion of this project, the plant returned to RoviSys to upgrade three more machines and are beginning efforts to upgrade equipment on an entirely new product line.