Mixing Fast Implementation with Long-Term Growth
Facing furnace failure and an obsolete control system, this float glass manufacturer required a full system modernization in record time to meet its aggressive production goals.
While performing routine maintenance, a leading North-Carolina-based glass manufacturer discovered that its furnace was failing and required an earlier than expected cold tank repair. Quickly, they also realized that that was only the start. The float glass production line needed a full control system modernization during the repair in order to successfully produce glass during its next 20-year campaign. The effort required meeting a lightning-fast design and implementation schedule for a solution that would fundamentally change production capabilities.

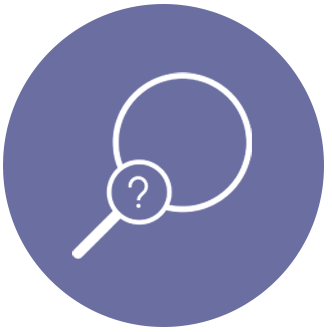
The Problem
A major control system upgrade like this typically requires two to three years of planning and implementation efforts. However, this standard project timeframe didn’t work for this plant—it needed the full system to be built and in-place in just 12 months.
This aggressive schedule was further complicated by the value driven production goals set by the manufacturer. To justify the project, it targeted a 5% increase in yield and a six-figure reduction in energy cost. These enhancements would be driven directly by the new process and control system.
The manufacturer realized it would have to devote all of its resources into getting the facility and the new production line ready for start-up, and it needed an automation partner that would work with them as a legitimate extension of its team.
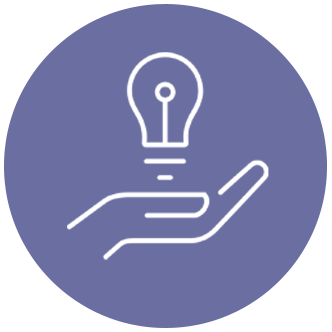
The Solution
The first step in the plan was to design a detailed project schedule that included each incremental task around these major milestones:
- Complete the design in three months
- Build and implement the new control system in five months
- Complete initial testing in 3 weeks
- Provide a one-week factory acceptance test
- Complete all commissioning activities in two months.
For the design, RoviSys selected the Siemens PCS7 v8.1 platform with three pairs of redundant AS410 controllers and ES drives for seamless SINAMICS drives integration.
RoviSys then designed a system architecture that provides redundancy from the operator stations and servers down to the controllers and communication channels, which helps ensure high system availability for the duration of the product campaign. The operating system and plant bus were also designed with redundancy built-in, following the goal to create a robust, high-availability system required for 24/7 operation.
In all, the solution covered all the project requirements, from functionality and ease-of-use, to maintenance and troubleshooting— all within the tight timeframe requested by the manufacture
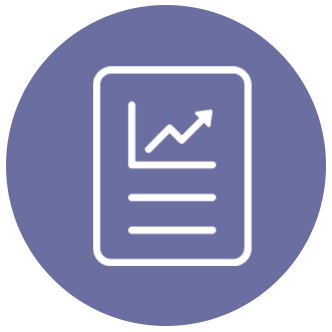
The Result
This glass manufacturer received more than they required at the outset of the project. The increased redundancy of the system has provided 100% uptime operation and improved diagnostics and troubleshooting capabilities.
Technicians now identify and solve problems faster, data flow through auxiliary systems is improved, and the plant has a built-in control system upgrade path that will eliminate the risk of future obsolescence.
Most importantly, these improvements were delivered while also meeting the core requirements of the job: Delivered on schedule, and surpassed previous production output within two months of launch. The manufacturer has met their energy savings target and exceeded the 5% increase in production yield goal.