Automating Process Perfection
For this around-the-clock glass manufacturer, aging hardware, lack of integration support and system robustness issues threatened the overall throughput of the plants operation. It’s time for an automation upgrade.
After cooled glass exits the lehr in this float glass manufacturer’s continuous process facility, the cold end team takes over. This requires careful inspection of the glass ribbon, scoring and snapping caps to precise measurements, and carefully conveying lites flawlessly throughout the process and into many packaging stations.
Maintaining the care and precision required to fulfill this side of the manufacturing process is a challenge in the best of environments. Doing so while keeping pace with a glass melting operation running 24 hours a day, seven days a week, 365 days a year can be beyond daunting.
To cope, this Brazilian manufacturer recently upgraded its core hardware to enable automation robustness and maintainability of the critical inspection, cutting, routing and material transfer processes required to deliver quality products to customers at the pace they demand.
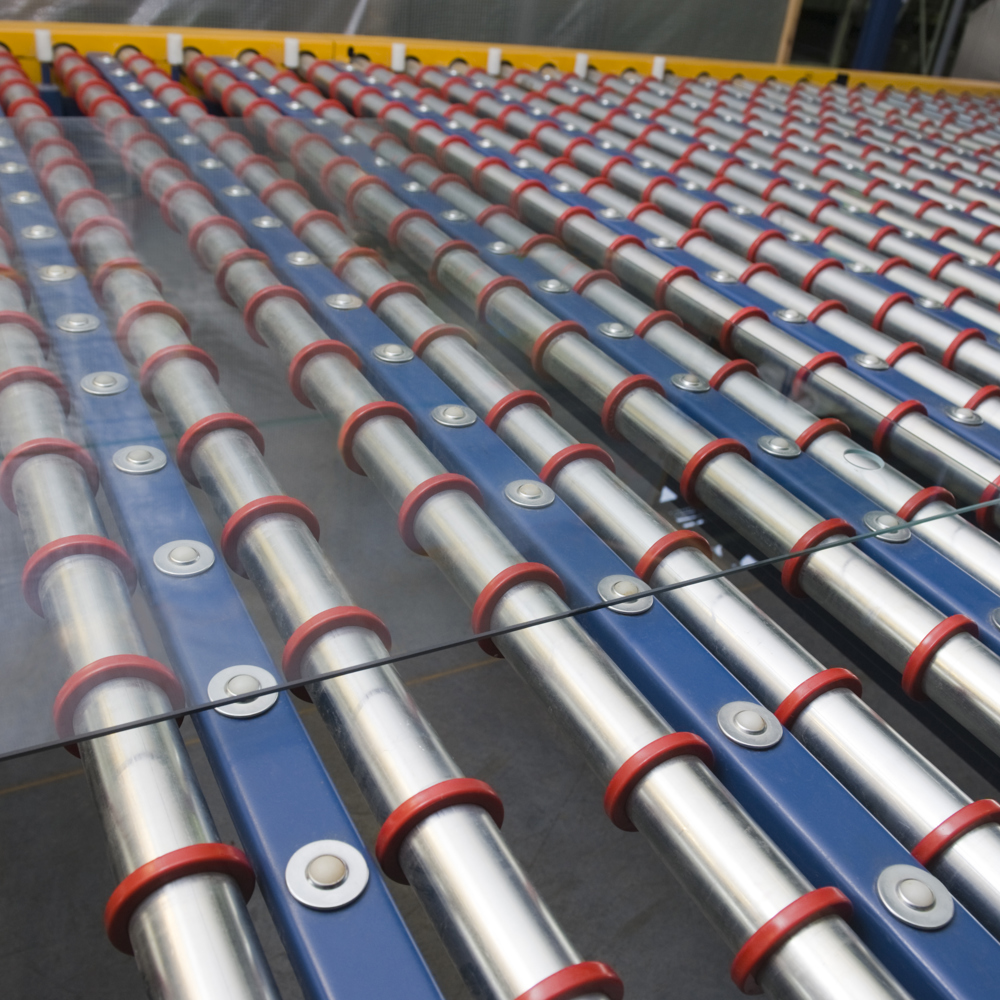
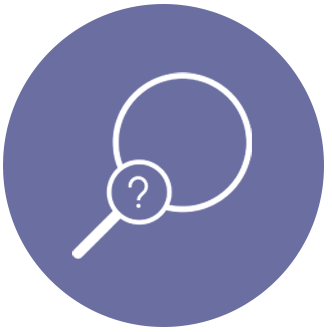
The Problem
The fundamental issue faced on the cold end side of this operation was the legacy,
custom-coded control system it relied on to complete each step of the process. The system was a quarter century old and using outdated interfaces that decreased operator efficiency and made adding new tools and equipment needed to expand plant
capabilities extremely challenging. Worse, the system depended on obsolete and hard to source parts and components, which put the plant at the constant risk of catastrophic breakdowns that could result in lengthy downtime and lost revenue.
The only course to overcome this issue was to overhaul the entire control system, replacing legacy controls and software code with a scalable, solid control backbone that could match the pace of the full business and allow for the growth and improvement it
needed.
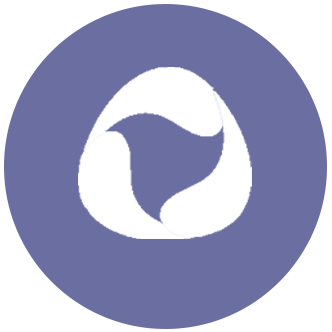
Our Role
A job this big requires the use of a broad range of technologies and automation solutions from an equally broad range of vendors and sources.
They include:
- Rockwell Automation ControlLogix
- GE Proficy iFIX HMI
- Pick-on-fly Kuka Robotics
- Dr. Schenk & ISRA Visual Inspection
- Coordinated motion of 30+ servo motors/drives
Success in this complex task is determined by the ability to coordinate these disparate systems into one seamless, efficient process. With over 30 years experience integrating
automation systems across the manufacturing industry, only RoviSys carries the broad range of expertise required to fill this role.
Results of this upgrade and modernization reversed risks associated with legacy products. The benefit - manufacturing sites total yield has increased by 3%.
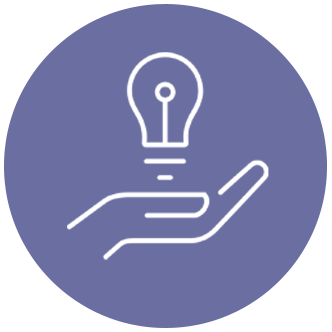
The Solution
The first step in this upgrade was to overhaul the legacy mechanical and controls hardware and replace it with a more modern, robust, and sustainable solution geared for the future. This included new mechanical equipment, a newly designed glass optimizing software, new controls platform and refined functional definition of the glass cutting, tracking, and routing process.
After the design was in place, RoviSys began developing the solution that would be installed at the customer site. During development, RoviSys was required to work with and integrate into other vendor systems ranging from Dr. Schenk Smart Cameras to Kuka robots and Bystronic stackers. During onsite installation and commissioning, RoviSys again worked alongside these vendors as well as the customer team to provide one seamless solution.
This newly designed system created not only a more efficient glass optimizing and cutting process, but also provided a detailed data trail throughout the site. This required careful collaboration and integration of each piece of the process and each distinct technology and tool it requires. RoviSys also developed an information bridge that tied production data into an existing customer MES solution. This bridge provided production data, defect data, and calibration data from the plant which allowed the customer to compare one manufacturing line to others. This information bridge enabled customer employees from all over the world to review pertinent information for this site and relate it to their facility.
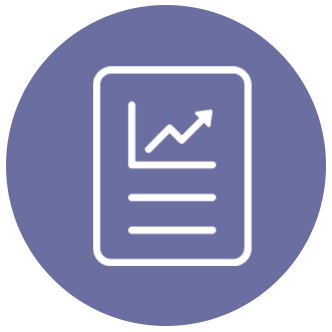
The Result
The glassmaker began this process facing a significant risk with the maintenance and maintainability of their primary control system—a legacy product composed of obsolete parts and which only one employee could successfully troubleshoot or repair.
The result of this upgrade and modernization project completely reversed this risk. The modern, state of-the-art components that make up this solution provide easy maintenance and offers the customer flexibility when adding new capabilities to the system. It also allows the plant to maintain more operational up-time, minimize downtime, and allow for additional employees to become system experts. These benefits have increased the manufacturing sites total yield by 3%.