Going Big To Reduce Scrap & Risk
U.S. Based plastic bag manufacturer partners with RoviSys for a legacy controls and information infrastructure upgrade. The result was a state-of-the-art, data-rich system that was up to the challenge of modern manufacturing.
A global acquisition provided this Missouri-based plastic bag manufacturer the capital it needed for a long overdue upgrade to its legacy controls and information infrastructure. The goal was to create a state-of-the-art, data-rich system that was up to the challenge of modern manufacturing. An undertaking like this required a partner with deep industry expertise and experience implementing large, complex information and controls projects.
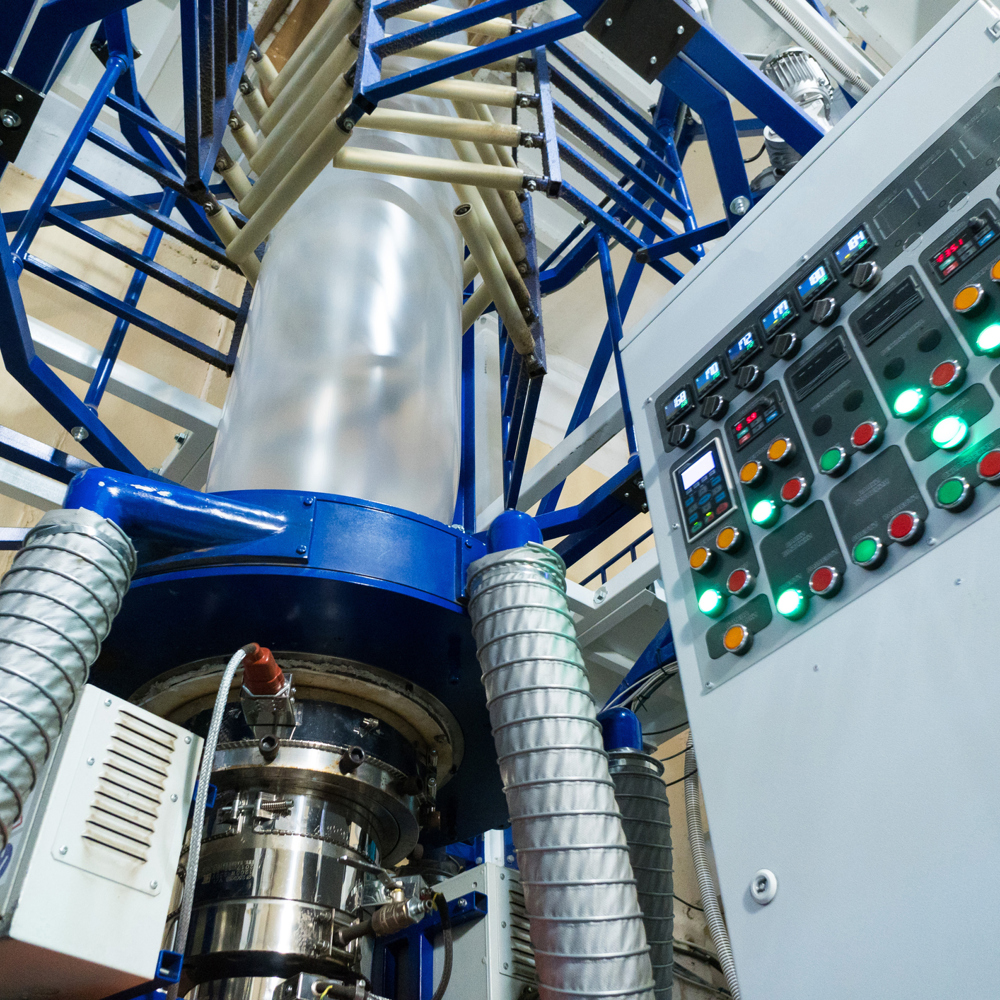
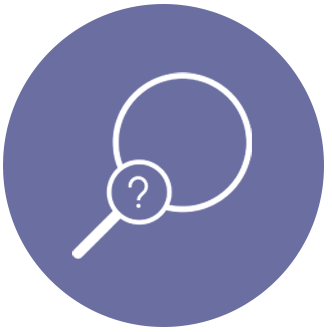
The Problem
This southern Missouri plant requires precise timing throughout every step of its manufacturing process to keep product flowing. Any interruption in the process results in hours of downtime and requires manual intervention for equipment cleaning and system reset. Plus, incomplete batches are problematic, and effect customers downstream.
The control system running this process was simply not up to the challenge of next generation manufacturing. The legacy system required continual operator interaction, resources, and man-hours to run. In this manual-labor heavy environment, inventory reconciliation was consistently 15 to 25% off, and the company was unable to efficiently and consistently calculate the scrap that resulted.
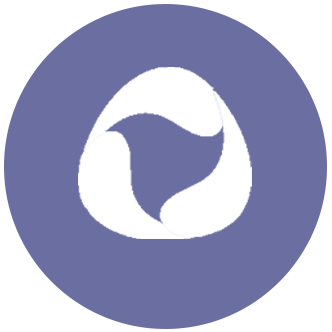
Our Role
To bring operations up to date, the company needed a partner with deep industry expertise and the bandwidth and creativity necessary to take on a massive overhaul of a supervisory batch implementation with a requirement for real-time, on-time delivery of product. After exploring the market and experimenting with integration competitors, the manufacturer found that RoviSys possessed the unique range of industry knowledge—from an understanding of the intricate extrusion and batching process to designing critical information flow— and experience with large-scale migrations needed to make the project a success.
Beyond automation implementation, this manufacturer utilized RoviSys to assess their existing system, gather project requirements, provide design guidance and strong project management to ensure that the final solution met the needs of the entire working group. From IT to plant floor to management, RoviSys acted as a catalyst to bring all stakeholders together.
Immediately, there was complete visibility into overall manufacturing process, with traceability to each individual material in every batch.
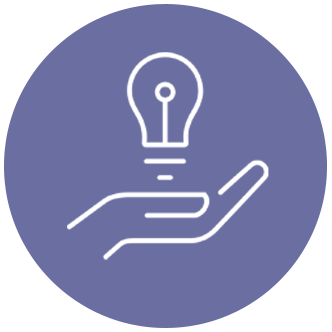
The Solution
The enterprise-wide nature of this effort made the initial assessment phase absolutely critical. With so many stakeholders, the first steps of requirements gathering, problem identification, site survey, interviews, and collecting information set up a foundation to build the right solution.
RoviSys interviewed everyone from global IT to operators and plant floor staff, from supply chain and raw materials experts to maintenance workers and managers—and created a comprehensive plan that accurately captured and addressed every unique requirement for each user at every step.
The result was a two-part solution.
1. Process Control: RoviSys crafted a supervisory batch solution around the challenges of the fast-paced resin delivery system, comprised of many shared pieces of equipment. Modern fault tolerant network topologies, connected devices, and distributed I/O were deployed to create a solid basis for robust operations and to enable continuous information flow. Leveraging the state-of-the-art plant floor infrastructure and the simplicity of the S88 model, RoviSys established an efficient and straight forward means for the convergence of the plant floor real time data with the enterprise ERP system.
2. Information Flow: RoviSys designed and developed a reliable data communication protocol using XML and RESTful web services to receive production orders, recipes, and inventory data from the company’s ERP system. Inventory consumption data from production would be automatically reported back to the ERP system to allow for accurate inventory tracking without any user interaction.
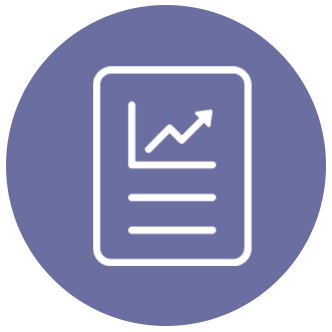
The Result
Once each component of the modernized solution was tested and ready, RoviSys worked directly with the plastics manufacturer to roll out the solution with as little disruption as possible. A five day window was allotted to get the first production line operating. RoviSys was able to bring the first line up in just three days, and within five days, five out of six of the total lines were running on the new system.