Custom Integration Solution Brings New Pipeline Online Fast
This U.S.-based oil producer with midstream operations on the Gulf Coast needed a quick-to-market control-systems solution to integrate a new pipeline into its existing infrastructure – with minimal disruption to its operations
The company was adding a new pipeline to support production of high-sulfur diesel fuel, which is used in boiler systems as well as locomotive and marine applications. In any midstream operation, maintaining the highest levels of safety, operational control and data visibility are paramount, and adding new equipment to the infrastructure needs to be planned carefully.
To ensure that the new pipeline meshed seamlessly with existing facilities, the project required a strategic automation partner with industry-specific experience – a partner that understands the needs of engineers, operators, maintenance staff and other key stakeholders, and how to get them on the same page.
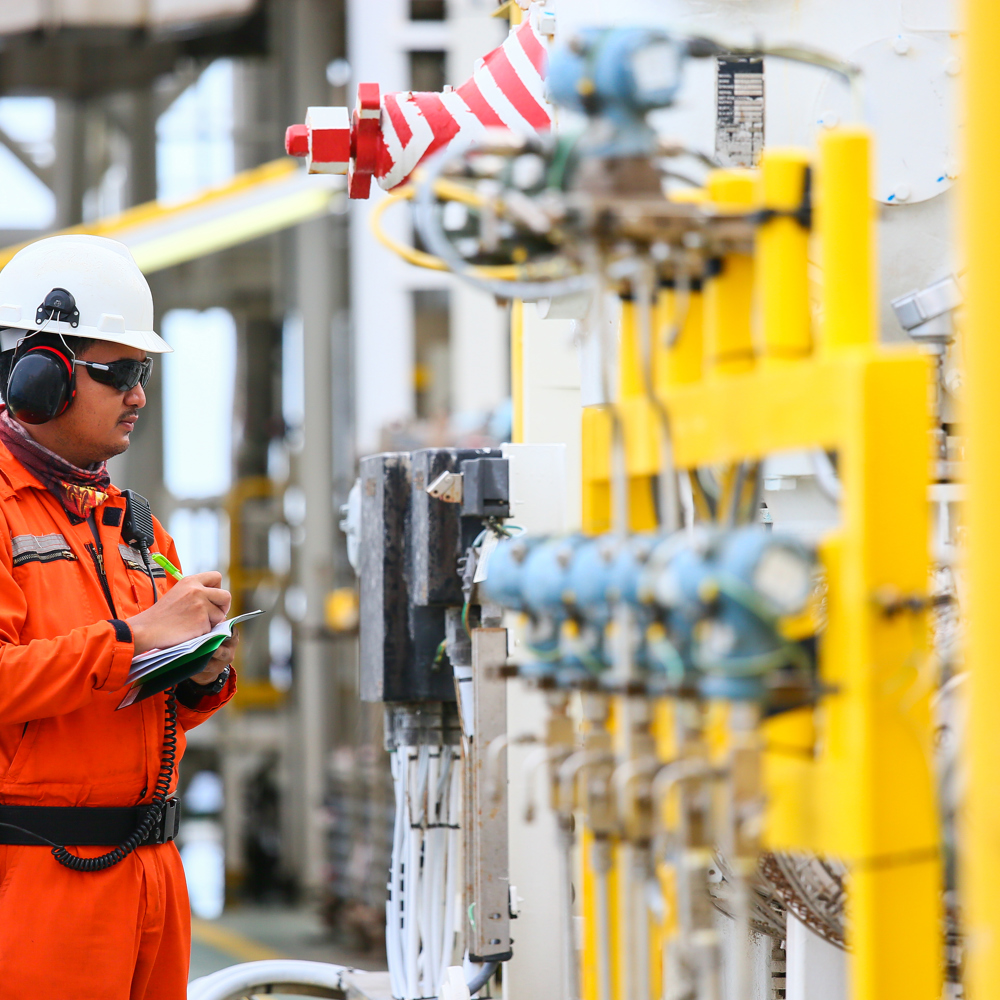
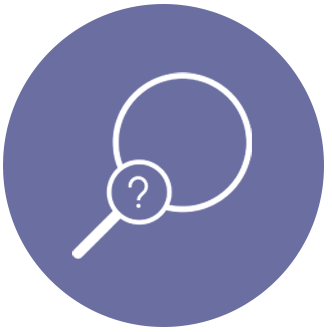
The Problem
Data is the lifeblood of midstream operations, and the entire network of facilities, equipment and control systems must be in sync. If there are gaps in the system, operational visibility is compromised. This oil company transfers product from a dock on the Gulf Coast to a tank farm, via a pipeline that connects many pumping stations along the way. Stations along the pipeline were running on a fragmented patchwork of control systems – some current, some out-of-date.
The main challenge was integrating a new, mile-long pipeline into the infrastructure, ensuring that the dock (Point A) and the tank farm (Point B) were seamlessly linked. Visibility into data and precise timing are essential to maintaining critical operational parameters such as optimal pressure in the pipeline.
The oil producer engaged a consulting firm to conduct a front-end engineering and design (FEED) study. In its recommendations, the FEED study failed to take into consideration the existing pipeline that needed to connect with the new pipeline. The company engaged RoviSys to identify any gaps in the study that could impede the safe and efficient integration of the new pipeline into the existing infrastructure. Specifically, RoviSys was tasked with determining if the new control-systems architecture would mesh with existing operational and business systems – or whether the company needed to implement new systems.
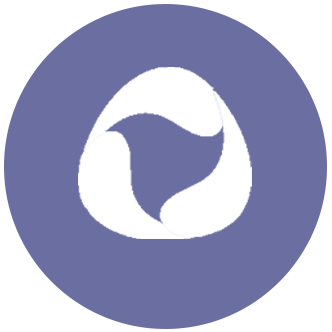
Our Role
To ensure that the engineering and design roadmap for the new pipeline would enable a successful integration of the new and existing pipelines, this pipeline operator needed a strategic partner that understands the unique challenges of the oil and gas industry. The project required a systems integrator with the experience, resources and methodologies to deliver a safe, reliable and cost-effective solution.
With more than 30 years of experience working with oil and gas companies, and an ongoing commitment to vendor independence, RoviSys was ideally suited to identify any gaps in the original FEED study, recommend solutions for a seamless integration and deliver results within a tight timetable. The RoviSys Oil & Gas team is well versed in translating between engineers, operators and other stakeholders who often seem to speak disparate languages. Plus, independence permits an unbiased, holistic perspective for evaluating and integrating dissimilar systems.
With RoviSys as a strategic partner, the company was able to integrate the new pipeline into its existing infrastructure in a matter of weeks.
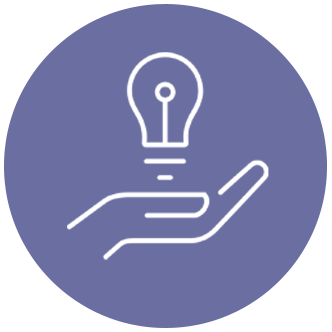
The Solution
The first objective was to conduct a comprehensive analysis of the existing equipment and controls-system software, which included thoroughly documenting all existing automation components as well as defining algorithms and safety parameters. With this
information, RoviSys was able to create a controls narrative document outlining an integration strategy that met all safety and operational requirements.
Ultimately, RoviSys developed a new control-system architecture that is integral not only to evaluating potential product costs, but also to anticipating equipment-performance issues. As part of the new architecture, updates and modifications were implemented to the existing HMI, PLC and other control software to ensure that the new and existing pipelines were completely in sync. An important element of the project was establishing interlocks to accommodate potential human error.
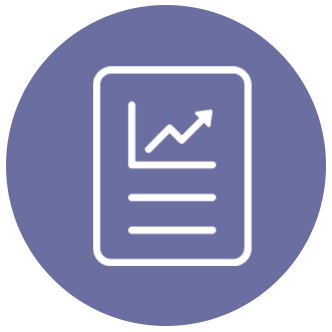
The Result
With RoviSys as a strategic partner, the company was able to integrate the new pipeline into its existing infrastructure in a matter of weeks. The pipeline, which boasts a maximum flow rate of 20,000 barrels per hour, has enabled the company to tap into a new market, and the new control-systems architecture has received positive feedback from its operations team, engineers and business partners.
The integration of its once fragmented control systems into a more unified framework has created information visibility that enables timely, intelligent decisions and operational flexibility for this pipeline operator.