Packaging
Packaging producer turns to RoviSys to improve quality, productivity, and efficiency data.
A disposable packaging maker was struggling to record vital productivity and efficiency data across its plants. RoviSys was challenged to update and overhaul data collection practices and automate information tracking systems without disrupting production.
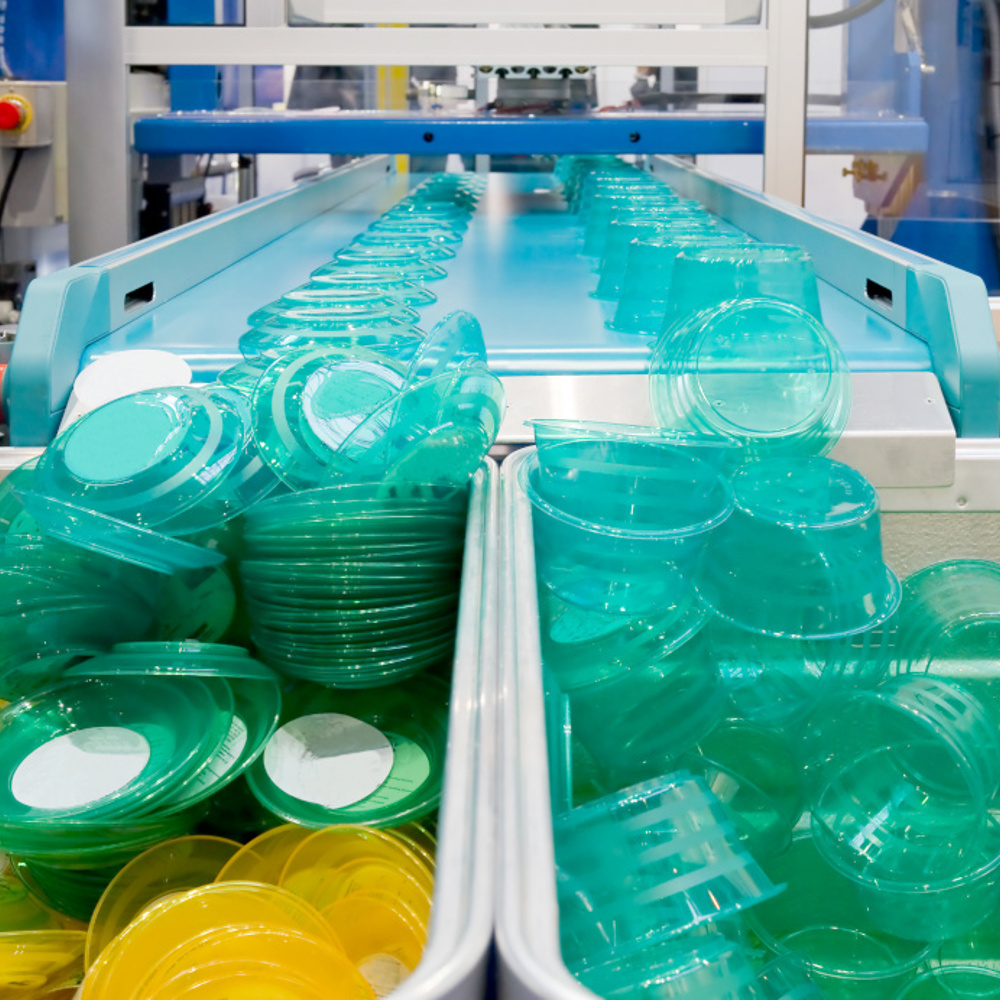
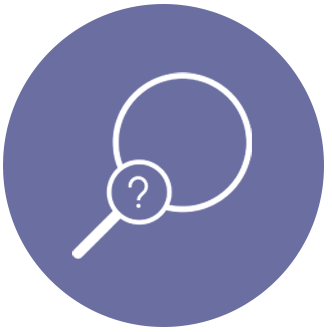
The Problem
Despite a product range spanning all the way from fast food containers to pharmaceutical packaging, the company relied primarily on manual recording of key production data and an expensive proprietary application to monitor quality.
With this broad range and multiple plants in operation, this recording strategy proved insufficient to accurately and consistently track global output or machine uptime. The packaging producer required a 21st century solution in place that would fully update and integrate its data collection system.
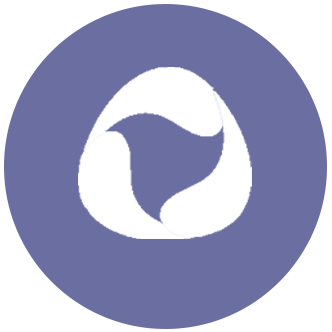
Our Role
Backed by a direct relationship with OSIsoft dating back to 1991, RoviSys brought 25 years of PI System implementation and custom software development experience to this challenge. The added benefit of an independent company with no ongoing licensing fees for its service, RoviSys proved to be the ideal provider to take on this data problem and enable the company to improve performance and increase profits based on real metrics.
Because of the company’s decision to implement the PI System at all their plants, RoviSys was able to focus on using the out of the box functionality of the PI System to implement as much of the solution as possible, only using custom development where necessary. As a result, the company was able to roll out the solution to their entire manufacturing network with only minor modifications needed to add different machine types used in the various plants.
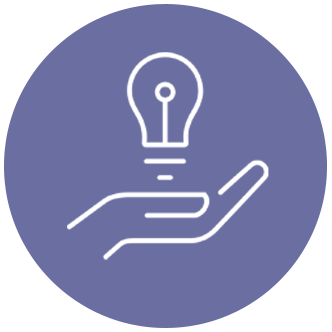
The Solution
To avoid disruption, RoviSys began with a pilot program in a sister plant following the same workflow as the current paper production data sheets. There, engineers installed a PI historian data collection system with a custom web application that allowed operators to more efficiently record standard production data and downtime details.
The system combined automated data collection from the machine PLCs with operator manual entry to build fully electronic production and downtime reporting. This data was transferred directly to the company ERP system through a custom interface removing the possibility of mismatching data between the data collection systems and the business systems.
With that in place, RoviSys was able to implement a full production analysis reporting system that accurately tracked production counts, OEE, and downtime pareto charts. Additionally, a quality module was implemented to allow operators to electronically enter their quality data from the floor in real time, using the same system as operators in the quality lab. This allowed quality data and production data to be combined into a single interface for analysis. And finally, to provide a single point of entry, portal functionality was implemented to allow other applications required on the floor—from order management to maintenance tracking—to be accessed from a single website.
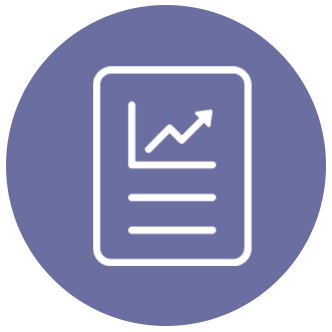
The Result
Once online, the packaging company received its first complete, accurate, and on-time data reports. The insights these reports provided allowed it to intelligently adjust production and OEE targets and helped increase uptime by nearly 30% in some plants.
It also translated into real-time savings by eliminating the licensing costs the company was paying for its legacy quality application. Planning for duplication also reduced the costs for reporting implementation at additional plants.