Positioning A Paper Mill For Sustainable Success
Production demands for Pulp and Paper manufacturers are growing at a rate that has never been experienced in the history of the industry. To revitalize one of its legacy U.S. paper mills, this global provider of paper and packaging solutions needed to give the facility a high-tech makeover.
In 2017, the company announced plans to install a state-of-the-art, 330-inch kraft linerboard machine and related infrastructure to replace three outdated, narrow-width paper machines. The new equipment would transform the facility into one of the lowest-cost kraft linerboard mills in North America, while adding new capabilities to serve a diverse mix of customers seeking more sustainable packaging solutions.
To help bring this massive capital investment to fruition, the company needed a trusted integration partner with a unique mix of industry-specific skills, expertise and resources.
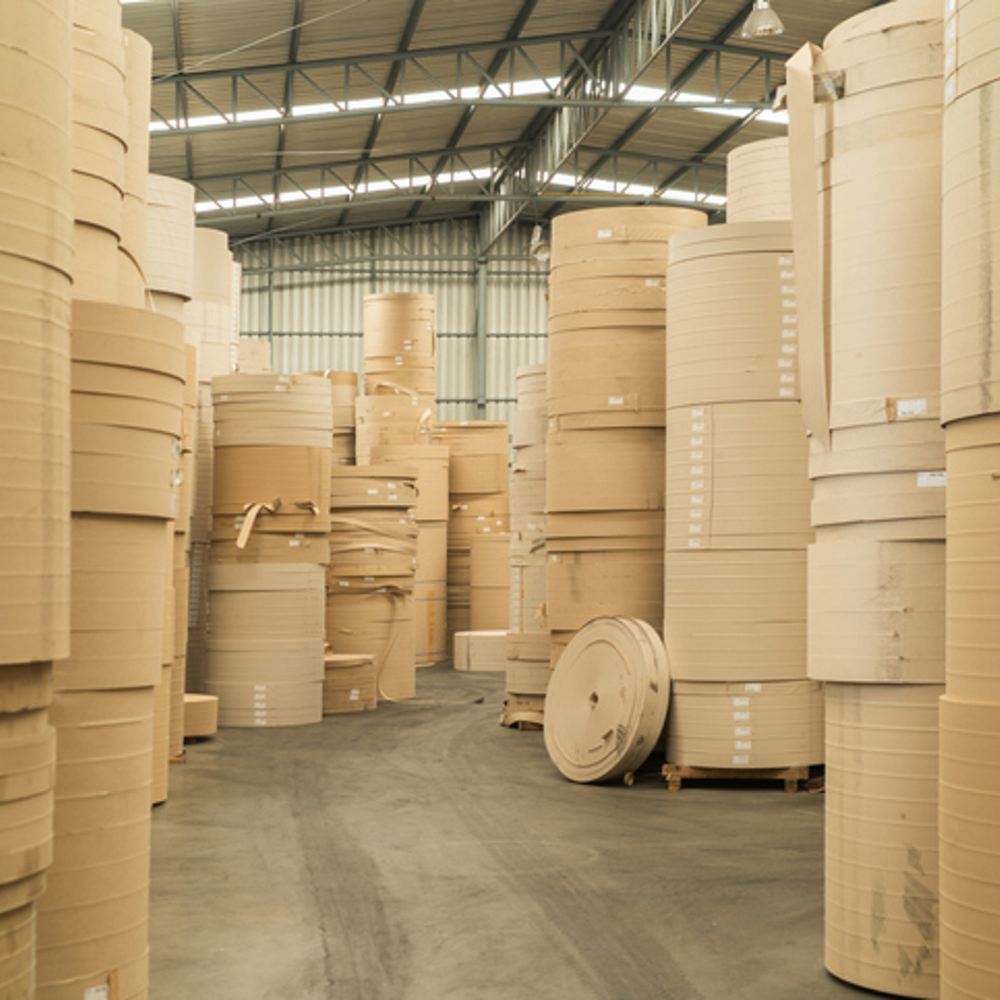
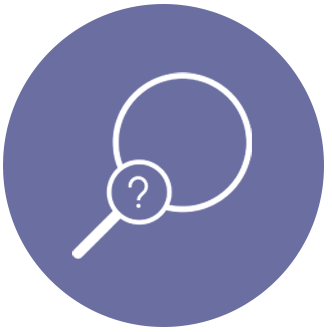
The Problem
This $400 million investment was a strategic decision to modernize a paper mill that had been in jeopardy of closure due to the extremely challenging business environment. With the installation of state-of-the-art equipment, the facility would have the capacity to produce more than 700,000 tons of kraft linerboard annually – for a variety of in-demand, sustainable packaging applications. Not only did the investment promise to expand the mill’s production capabilities, but it also would make the facility more efficient and profitable.
In order to achieve the production objectives that had been set for the new state-of-the-art paper machine, the company recognized that an additional capital investment would be required to provide process upgrades on the back side of the mill -- most notably in the Pulp Mill, where legacy pulp washers and a legacy electrical infrastructure would need to be replaced to meet the production requirements for the new paper machine.
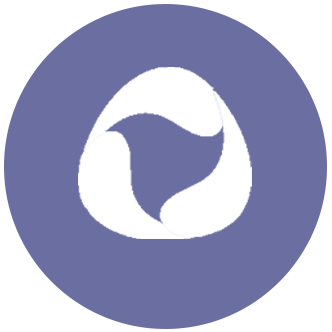
Our Role
For this customer, it is standard practice to select contractors for E&I Design projects through a public bid process. When all the bids were evaluated, RoviSys was the clear choice to execute the E&I design work required for replacement of the Pulp Mill washers and associated electrical infrastructure
With decades of boots-on-the-ground experience in the Pulp & Paper industry, long-term relationships with the leading industrial hardware and software vendors, and ample resources to provide on-site design expertise during a challenging time, RoviSys checked all the major boxes. Plus, this customer had engaged RoviSys at the mill for a previous project, and knew that RoviSys was more than capable of delivering a successful outcome for this complex endeavor. RoviSys was uniquely qualified to provide the top-to-bottom, front-to-back E&I design for the Pulp Mill.
The mill currently produces more than 700,000 tons of packaging material annually – an average of nearly 4 million pounds per day.
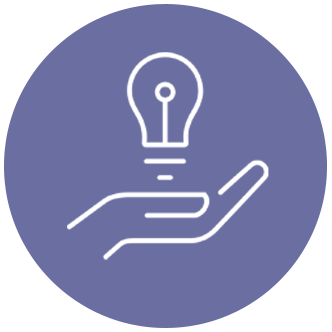
The Solution
As the first step in executing the E&I Design effort, RoviSys engineers spent multiple days on site at the mill -- walking down the current Pulp Mill infrastructure, tracking down and pulling legacy (and outdated) drawings, making corrections to legacy drawings via field annotations, and meeting with key electrical engineering personnel from the client’s in-house team to frame-up specification documents for the overall project.
Once the customer approved the specification documents, RoviSys embarked on a well-defined path to generate all drawings and documentation required for a comprehensive E&I Design Package that the client ultimately put on the street as a bid package for the Pulp Mill washer replacement project. The E&I Design package included all Motor Elementary and Loop drawings required for upgrade of the Pulp Mill, required drawings and specifications for new Motor Control Centers (MCCs), Cable Schedules for the Electrical contractor, and detailed Bill of Material (BOM) documentation for all components that needed to be procured to complete the installation. In addition, RoviSys designed a new Emerson DeltaV CHARMs system for consolidation of all DCS controls required by the Pulp Mill upgrade.
RoviSys met with prospective bidders and served as the liaison between the Mill’s electrical engineering staff and the selected Electrical contractor. To ensure that the project was implemented without design issues, the client awarded RoviSys a follow-up contract to oversee the work of the Electrical contractor during the implementation phase.
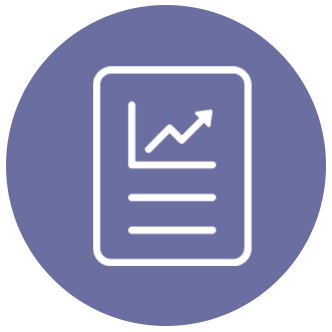
The Result
With new pulp washers and an upgraded E&I infrastructure in the Pulp Mill, along with a new Emerson DeltaV CHARMS controls solution for Pulp Mill operations, the site now has a robust architecture to support continued growth and an accurate baseline for future upgrades.
The mill currently produces more than 700,000 tons of packaging material annually – an average of nearly 4 million pounds per day. For a high-volume plant such as this one, reliability is absolutely critical. Just one day of equipment downtime costs the company as much as $1 million in lost productivity.
With the mill’s production equipment and controls infrastructure modernized and optimized, the facility is well-positioned to deliver sustainable paper and packaging solutions and make meaningful contributions to the company’s top and bottom lines.