Real Time Material Tracking For Parts Manufacturing
A U.S-based manufacturer of parts relied on a manual crane operation process within their facility, with little oversight and minimal data for identifying production downtime and operator efficiency. The company needed a solution to display real time locations of assets and materials, and to provide historical records identifying quality issues and reasons for downtime.
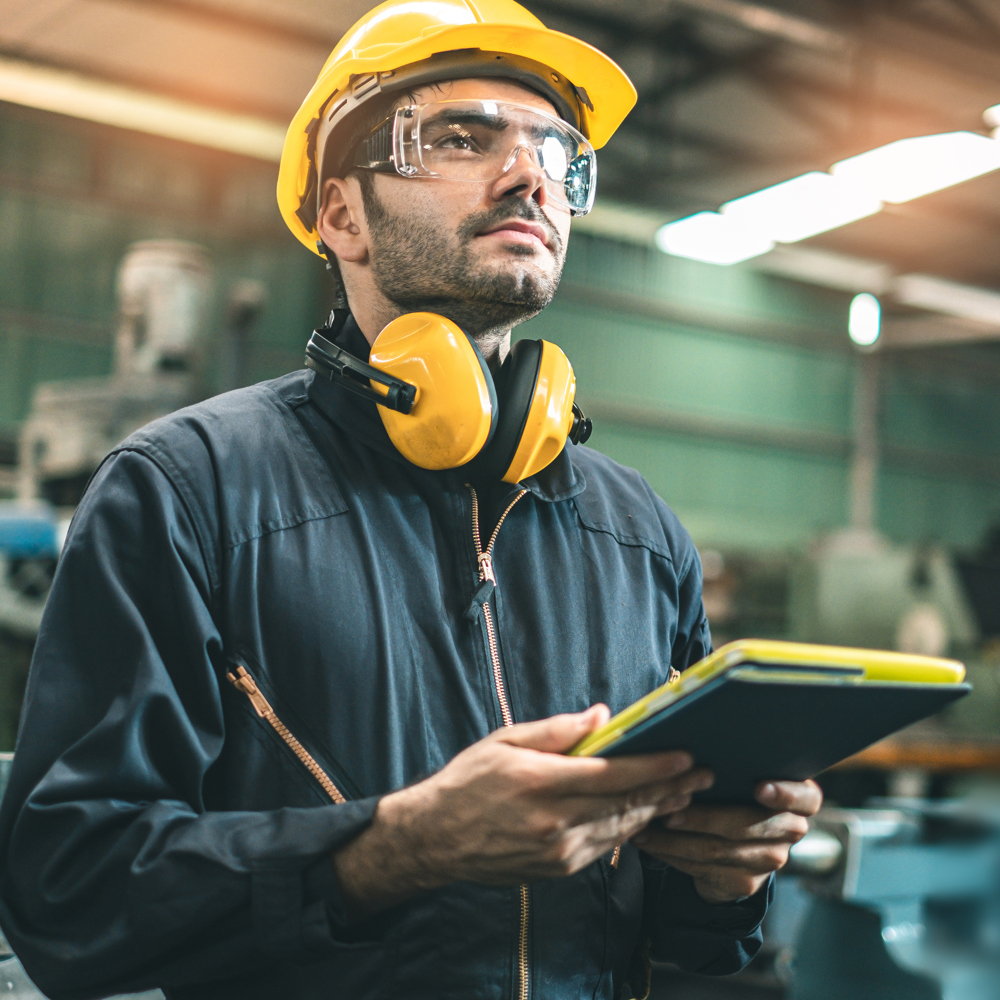
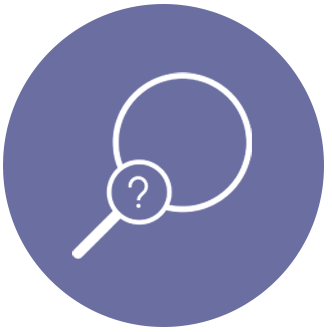
The Problem
A customer with a manufacturing process that required the use of manually operated cranes to move material between treatment processes was lacking real time visibility and historical tracking. The sequence and timing of asset movement is critical for product quality, and issues were common due to lack of visibility and delayed accountability.
In addition, equipment utilization and operator performance was untrackable without accurate history of crane position and movement. It was critical to ongoing growth for each asset to be tracked individually. In addition to the technical challenges involved, the manufacturer required a rapid solution that would connect to their existing MES.
A timeline of two months and a $100K budget was available for the effort.
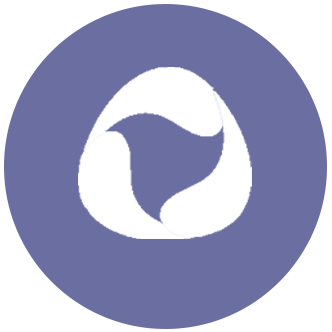
Our Role
The ability to solve tough technical problems and integrate solutions for systems with off-the-shelf and custom software positioned RoviSys perfectly to design and implement a solution for this manufacturer.
As a vendor independent solutions provider, RoviSys was free to fully consider all available solutions, and select the option best suited to this effort. A proven track record of executing projects on time and under budget provided added confidence for this aggressive budget and deadline.
RoviSys delivered an innovative solution that integrated the manufacturer’s existing MES solution with OSIsoft PI and RFID, and proved reliable.
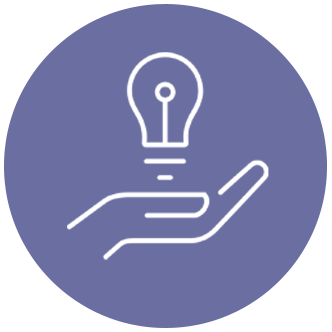
The Solution
RoviSys initiated an assessment and identification phase, working with stakeholders to review existing systems, identify deficiencies, and determine goals. RoviSys proposed two solution options that met requirements and replaced existing tracking equipment. The chosen approach introduced RFID, not previously considered by stakeholders, but enticing because of cost savings and benefits that exceeded defined goals and eliminated deficiencies. The solution included a combination of off-the-shelf technology and software design.
Specifically, RoviSys identified an opportunity for a Real Time Location System (RTLS) using Active RFID. The system was based on a matrix of PoE ‘anchors’ throughout the production area, which received Time Distance of Arrive (TDoA) signals from wireless tags mounted on assets.
To expose the RTLS data to the existing OSIsoft PI data historian and tie into MES records, RoviSys built a service to read 3D location data (including acceleration and orientation data), then push to the OSIsoft Asset Framework**. This allowed for simple configuration of additional assets and RFID tags. The solution exposed status and location of materials throughout the production area. Wireless capability allowed for placement of tags wherever required. Real-time battery levels of tagged assets were pulled into OSIsoft PI, and notification emails triggered when batteries required charging.
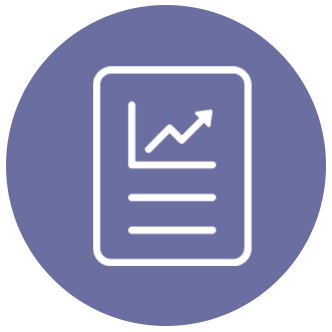
The Result
RoviSys delivered an innovative solution that integrated the manufacturer’s existing MES solution with OSIsoft PI and RFID, and proved reliable. Prior attempts to use traditional crane location tracking instruments in the facility’s harsh environment had failed. With the RoviSys solution, asset position information was accurate within a 1-2 foot range, overall system reliability increased, and business and operations stakeholders gained valuable insight which eliminated delay and increased throughput.
Most importantly, these improvements were delivered while also meeting the core requirements of the job: On schedule and within budget. Benefits were realized immediately and this solution has been duplicated at additional customer plant locations.