Rebuilding A Legacy: Uptime, Safety, & Sustainability
Big Three automaker operates in aging, 20th century facilities relying on legacy building control systems that have run far beyond their useful lives. To improve comfort and safety of operators and reduce the plants’ environmental footprints, the automaker needs to give these systems a 21st century update—but it must do so without disrupting production.
The facilities at the heart of this Big Three automaker’s production are essential pieces of its streamlined and efficient North American operations. However, while the flow and lean production systems may be optimal in these customized factories, the decades-old building controls within them were not— which took a toll on both the workers and the environment.
To correct this, the automaker needed to find a difficult balance: to update these manual, legacy systems, but to do so without stopping or slowing critical production.
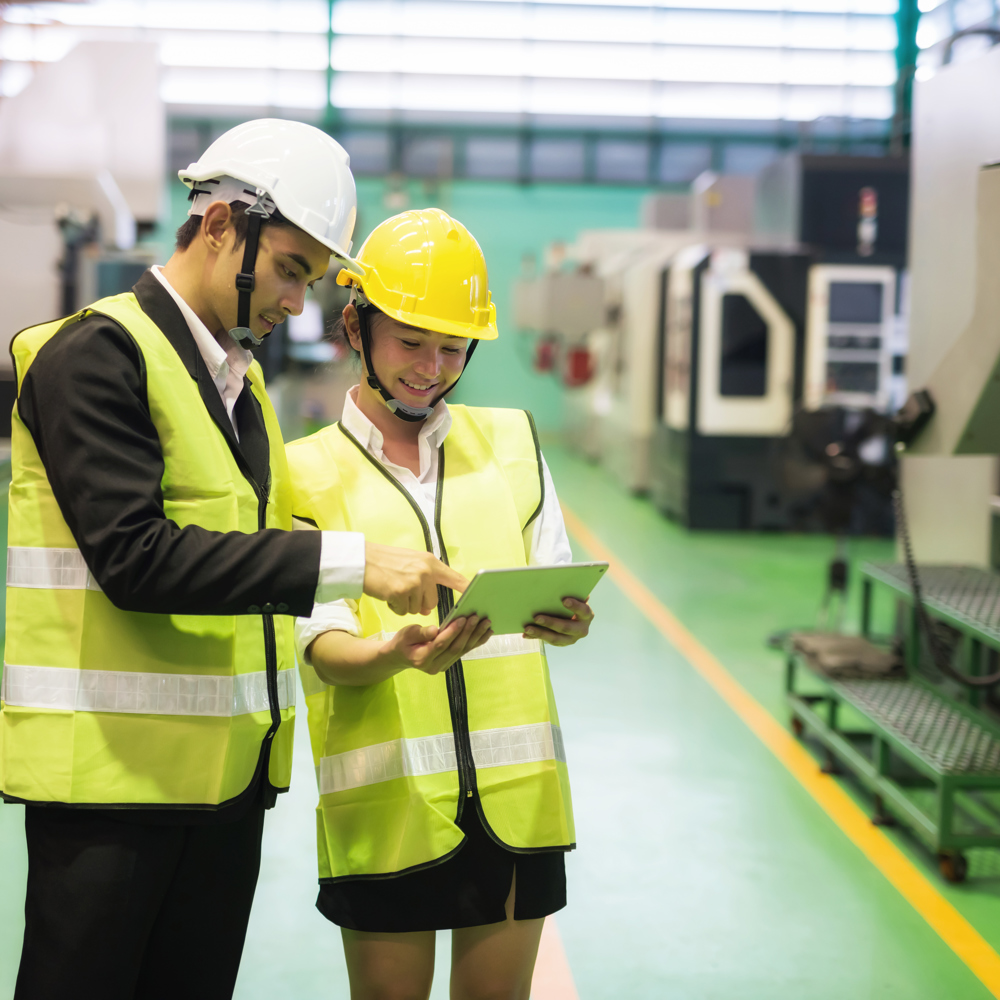
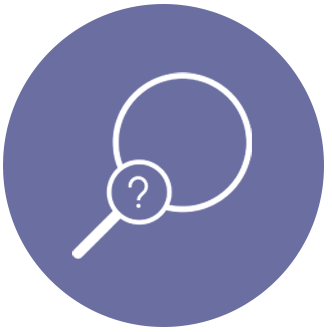
The Problem
The aging structures of eight facilities across North America—including active manufacturing plants and corporate office space—relied on building and climate control systems that were more than 20 years old. These systems included minimal automated controls and had neither been standardized nor maintained. As a result, they were exceedingly unreliable and required frequent manual intervention to repair. Compounding the challenge was the fact that minimal documentation, control narratives, control drawings, or equipment schedules existed for these legacy systems.
The challenge was further complicated by the sheer volume of production in these facilities and value created per hour of operation. A single minute of downtime in these plants can cost the automaker up to $10,000. So, the automaker needed a Master Systems Integrator that could not only perform the core tasks of modernizing all HVAC unit controls and custom air handler control systems and incorporate automation to formerly manual operations, but one who would do so without disrupting production.
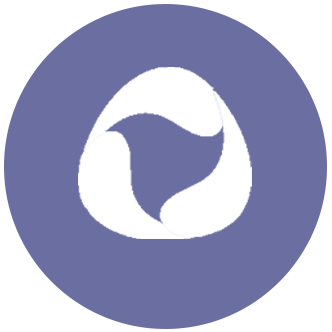
Our Role
To accomplish this, the automaker needed more than just a building controls specialist or a system integrator. To achieve the careful balance this project required, it needed a Master Systems Integrator with proven automation expertise with experience in
project and operational strategy as well as in control systems and software. A true partner that is capable of creating standards, documenting and delivering full-scale integrated control platforms with usability and ease-of-use as a priority, and working within the
needs and constraints of the plants’ core operations.
This is exactly where RoviSys surpasses the competition. With 30+ years of experience in automation and controls, RoviSys is renowned for its ability to tackle the most difficult puzzles, consulting with every level of the organization—from the C-suite
to the plant floor to ensure an intuitive solution that end users will quickly adopt and willingly use.
With 30+ years of experience in automation and controls, RoviSys is renowned for its ability to tackle the most difficult puzzles, consulting with every level of the organization—from the C-suite to the plant floor to ensure an intuitive solution that end users will quickly adopt and willingly use.
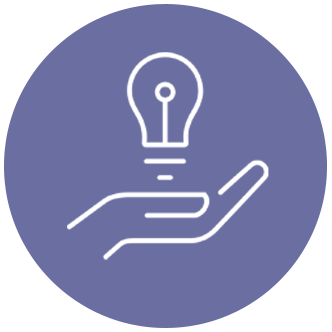
The Solution
As the Master Systems Integrator for this project, the first challenge RoviSys faced was to fully understand the needs and expectations of the manufacturing and sustainability groups, creating a complete and robust strategy that balanced demands from both the enterprise-level executives and plant- level executives to improve working conditions, decrease environmental impact, and do so while working exclusively within shut-down hours.
Based on these discussions, RoviSys selected the Tridium Niagara 4 platform, which integrated seamlessly into the existing control architecture. From there, RoviSys was tasked with creating the
necessary hierarchies, tagging dictionaries, and standard programming object blocks that would drive the system. This process included conducting a detailed architecture analysis of each plant and facility and critical front-end engineering design studies to properly outline the necessary means to optimization and automation.
A team of five dedicated engineers and a project manager were allocated to this task, working with individuals and specialists from the automaker for over six months to develop and perfect the FEED study. RoviSys delivered detailed site acceptance documents
and procedures that summarized every facet needed to keep the system running. Everything from factory acceptance tests and documentation to 100% complete user guides to hands-on/on-site user training and ongoing support was delivered.
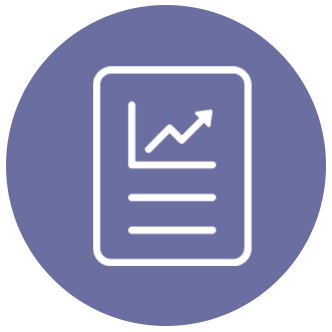
The Result
The final result of this project couldn’t have been better: the automaker received exactly what was expected, on time and under budget. It gained control and visibility into its building equipment,
which set the foundation for long-term savings and sustainability across its facilities, without incurring any unscheduled downtime in the process. With this solution in place, it has reduced its emissions by 25% for over 1 million cubic feet of production facilities.
But that isn’t all. During the implementation process, RoviSys engineers discovered 200-500 pieces of ancillary heating equipment at each plant that was either broken or not communicating—systems essentially left to “rot” because the process required to re-wire and replace them was deemed too expensive and required too much downtime.
Though this was clearly outside the scope of the original project,
RoviSys engineers discovered and recommended a simpler and less-disruptive solution to address this issue: connecting these devices wirelessly to the underlying system—a solution that ultimately saved considerable time, costs, and complications in the overhaul process.