Taking Control
An outdated control system was preventing this pharmaceutical manufacturer from bringing critical new drugs into production. To serve its market and its patients, the company needed to rebuild from the ground up.
The initial phase of conceptual design work for this project was taken on by another solution provider. But the pharmaceutical maker quickly discovered that this competitor lacked the capacity, manpower, and expertise necessary to effectively execute the project.
A two-week scoping exercise with a RoviSys project manager and engineer at the plant was all the company needed to understand that RoviSys possessed all of these required assets (and more) to take on this massive, delicate job.
Stymied by an unreliable, aging control system, this manufacturer of critical therapy drugs for chronic health conditions and diseases was unable to effectively introduce new products into its California facility. To meet the demands of both the patients that depend on its products and the strict industry regulations, the plant needed a full system reboot.
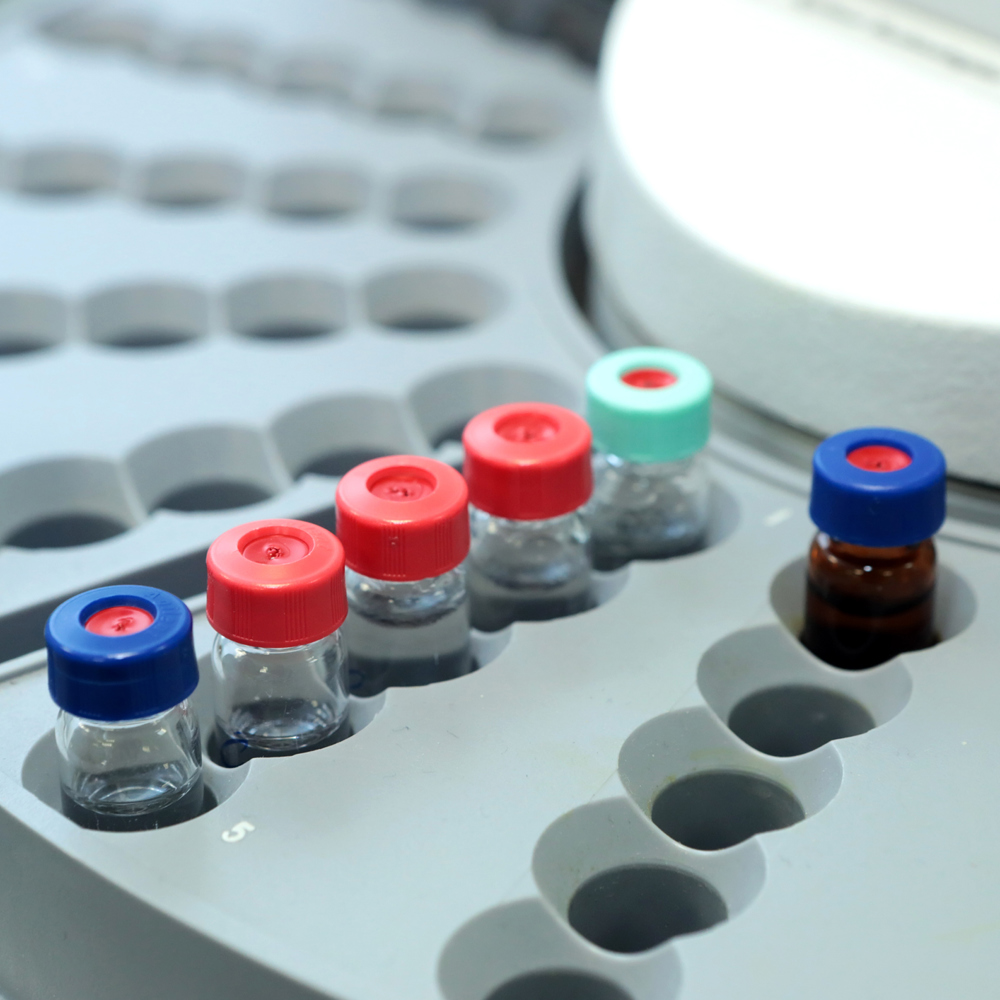
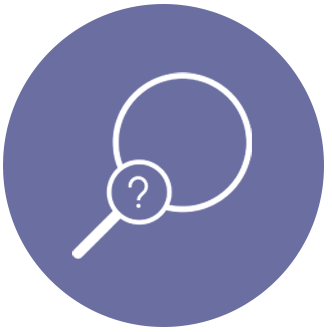
The Problem
In the heavily-regulated pharmaceutical industry, the manufacturing processes for every new drug, medicine, or product requires fresh validation independent of any legacy processes or approval.
The facility managers at this facility knew that the existing control system and process infrastructure, depending on largely manual processes and difficult to replace, obsolete parts, was too prone to reliability issues and manufacturing risks to consistently produce the results required to validate a new process.
To serve its market and bring much needed new products into the facility, this drug-maker required a new control system that migrating everything from cell culture fermentation processes to paper-based standard operating procedures into an up-to-date system that was consistent and reliable enough to grow with the industry.
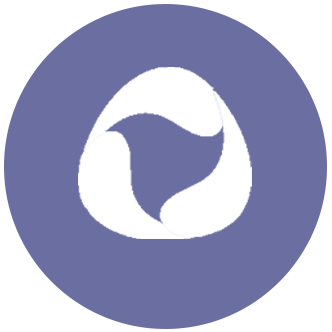
Our Role
The initial phase of conceptual design work for this project was taken on by another solution provider. But the pharmaceutical maker quickly discovered that this competitor lacked the capacity, manpower, and expertise necessary to effectively execute the project.
A two-week scoping exercise with a RoviSys project manager and engineer at the plant was all the company needed to understand that RoviSys possessed all of these required assets (and more) to take on this massive, delicate job.
Between the new automated functions and the overall design of the system, the company increased their production by up to 25%.
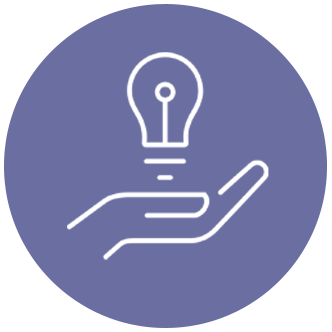
The Solution
RoviSys began with a rapid prototype, DeltaV system designed to prove the proposed architecture and controls philosophy that would define the solution. It also provided an opportunity to allow stakeholders at the facility to see and “feel” how the end solution would operate.
Pulling in up to 25 engineers for the project—including three senior DeltaV subject matter experts on fermentation, CIP, and system admin—RoviSys designed and implemented a complete control system overhaul for the drug maker in just 12 months.
In total, the overhaul included:
- Automating five plant bio-reactors and one CIP skid
- Designing and administering the virtualized DeltaV environment
- Implementing an equipment use log into the electronic SOP system
- System support for factory acceptance testing of equipment at six vendor sites
- Supporting commission and qualification activities.
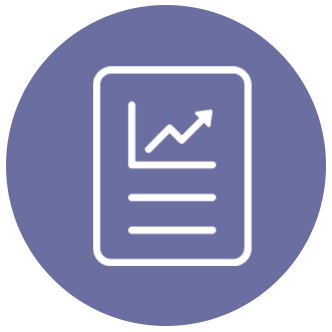
The Result
The primary goal for this project was to create a system robust enough to allow new clinical and commercial products to be easily introduced to the facility. Upon completion, the plant had the ability to manufacture multiple products in a suite originally designed for just one.
But this wasn’t the only success.
The new system allowed data from each process to be directly attached to the exception based batch record. By automating this previously hand-transposed data, the plant was able to significantly decrease the risk of human error. These electronic batch reports also provided a significant step forward in the plant’s digitization journey, allowing it to both keep pace with industry standards and better meet customer expectations.
And, between the new automated functions and the overall design of the system, the company increased their production by up to 25%.